How To End The Time Your Delivery Drivers Waste Searching for Packages
October 10, 2024
The last-mile delivery process needs to be made more efficient for both the company and the driver. If you apply a “First Principles Thinking” to the process, you’ll quickly recognize that a lot of the delivery person’s time is wasted on the non-essential activity of searching for packages.
If you’re not familiar with the First Principles concept, it’s a method of analysis in which you break down a complicated problem or process to its basic elements to find a solution. Based on a First Principles analysis, the essential tasks of a last-mile delivery driver is to load the right packages into the vehicle, drive to the customer’s location, and then deliver the items to the customer. All other activity such as searching for packages is non-essential to the core mission.
Time Breakdown of A Driver’s Workday
When you examine how package delivery drivers spend their workday, you’ll find a lot of their time is wasted on searching for packages. Our time-study analysis of a last-mile delivery driver’s workday found that more than 50 percent of his or her time is spent on locating packages.
Here’s what our study found:
• The average delivery driver travels 40 to 50 miles per day. That takes approximately 1.5 hours.
• A driver averages 150 stops per day with each stop taking 20-30 seconds. That time amounts to a total of 1.5 hours per day. (We define a stop in our study as the driver getting the package from the vehicle, dropping it off at the designated spot, and then returning to the vehicle.)
Those two activities add up to 3 hours. The remaining 5 hours in an 8-hour workday are spent on activities such as sorting, organizing, picking, verifying package information, and checking the personal digital assistant (PDA.) These activities should be classified as time spent directly or indirectly on locating packages.
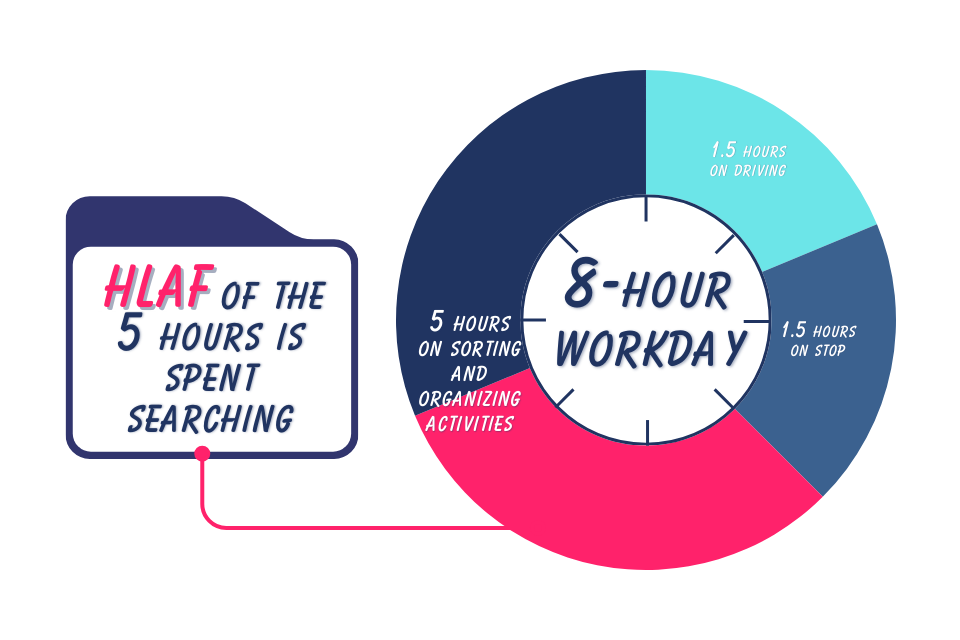
Therefore, based on our study, it’s safe to say that at least half of the driver’s workday is spent on the non-essential activity of searching for packages. When drivers waste time looking for packages in a delivery vehicle, it means they’ll make fewer drop-offs during a day. Moreover, the repeated searching for packages during the day takes a physical and mental toll on the delivery person.
Clearly, there’s a need to minimize the time a drivers spends looking for packages.
The Two Main Methods Used By Drivers For Finding Packages
Currently, the shipping industry uses two primary methods for package placement in a delivery vehicle.
- Method One: Packages are loaded and placed directly in the vehicle in specific locations without bags.
- Method Two: Packages are organized and loaded in bags based on delivery routes or zones.
The following table compares the time spent on finding packages for each method.
The Two Main Methods Used By Drivers For Finding Packages
Packages loaded in designated locations | Packages loaded in bags | |
---|---|---|
Time spent finding packages in the vehicle | Required after each stop | Required after each stop |
Time spent checking the delivery phone or PDA | Time-consuming | Time-consuming |
Time spent organizing packages daily | 2-3 times a day | Opening bags and organizing packages |
Round-trip time caused by not finding packages | Occasional round trips | Round trips due to packages of similar addresses in different bags |
Time lost due to phone crashes and restarts | May occur | May occur |
Time spent searching manually to avoid trips | Not needed | Requires manual search to avoid trips |
Time spent in the warehouse organizing packages and applying delivery number stickers | Not applicable | Time-consuming |
To make package identification faster and more visible, workers often rewrite the delivery number with a large, black marker. This process is not only slow but also prone to errors, further hindering efficiency.
Our Revolutionary Technology Speeds Up Finding Packages
We at Lotwork have developed an intelligent labeling system as a solution to the problem of wasted time in locating the right package for delivery.
Instead of relying on a label for item identification, each package is equipped with a Hyco wireless light tag that provides an audio-visual cue to its whereabouts. These tags are attached to packages during the pre-loading process on delivery trucks. When a driver arrives at the delivery destination, the tags provide audio and visual signals so the driver can locate packages in 1 to 5 seconds without having to waste time searching for the correct items in the vehicle.
Not only does our solution improve efficiency in last mile delivery, it offers a faster, safer, and more cost-effective approach for a delivery driver to find the customer’s package in a vehicle.