How We Went From A Prototype For A Ring Scanner To A High-Quality Product
October 18, 2024
It’s very common for startups and innovation-driven companies to launch a prototype for a market need but then find it hard to refine it into a high quality product that truly satisfies that need. It’s a stumbling block I wanted to avoid in bringing our Hyco ring scanner to market for logistics, manufacturing, and commerce.
The Five Basic Standards For Any Ring Scanner
More than a decade ago I saw a market need for a small, lightweight ring scanner that would be more ergonomic and worker friendly. To define the basic standards and minimum requirements for such a scanner, I applied the First Principles concept, a method of analysis in which you break down a problem into its fundamental elements to find a solution.
Here are the five basic standards I came up with 15 years ago for the ideal workplace ring scanner.
- No fatigue after 8 hours of continuous wear: Based on extensive user feedback, I concluded that the device should weigh no more than 20 grams.
- Battery life of at least 18 hours: This allows for continuous operation across two shifts in factories and logistics operations and even still have some remaining charge in the battery.
- Comfortable wear: The scanner should be easy for workers to wear and remove, cause no skin irritation, and ensure comfort throughout use.
- Breakaway safety: In cases of emergencies, the scanner should easily detach to protect the user’s fingers.
- Durable design: The device must withstand drops from three meters and have a water and dust resistant rating of IP66 or higher.
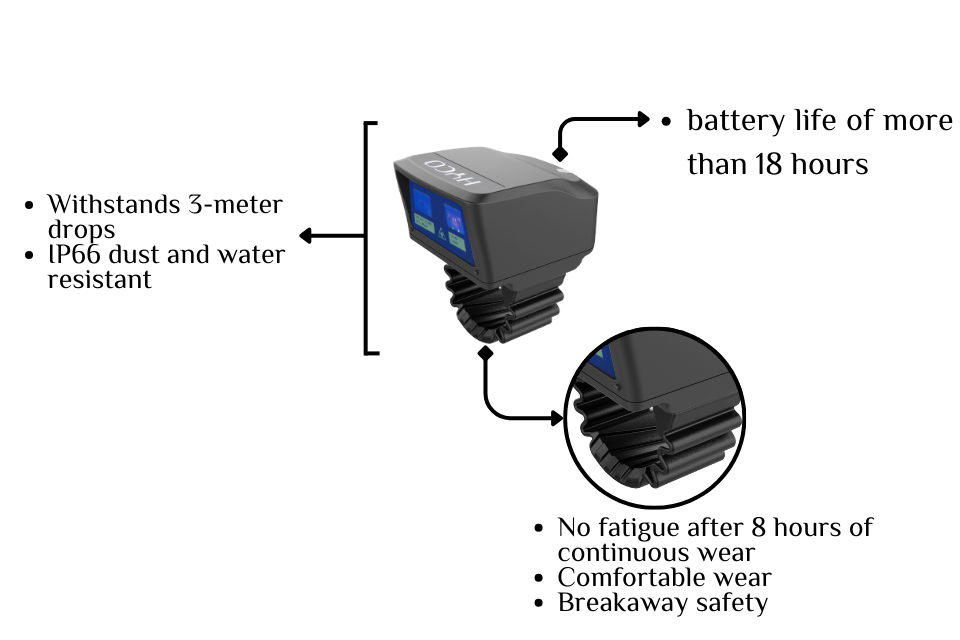
W26 ring scanner
Low-Power Consumption Technology Required
With those five standards in mind, I began looking around for the technology to make my ring scanner a reality. But I found that the low-power consumption technology required to achieve both small size and extended continuous operation for the envisioned scanner, while still meeting industrial standards, was not available.
That realization drove me to begin work on developing the necessary technology at Hyco Technology, a company I founded in 2009 in China. After much effort Hyco was able to develop this low-power technology, making it possible to reduce the scanner engine’s power consumption and allow for the tool’scontinuous operation over extended periods.
It took us only four years to develop a ring scanner prototype. However, it took us ten more years to refine the product to the high-quality version now that Lotwork presents on the market today.
Our W26 ring scanner meets the five criteria that I set out. It weighs just 20 grams (.07 ounces) and offers an impressive battery life of more than 18 hours on a single charge. It has been designed to handle the rigorous demands of industrial use, with a peak power consumption of 30milliwatt (mA) during scanning and an average of 5mA in active scanning mode.
This power efficiency allows the scanner to operate continuously for more than 18 hours with a scanning interval of every 3 seconds while meeting high industrial standards such as a 3-meter drop resistance, an IP66 rating, and over a 30 kilovolt electrostatic discharge (30KV ESD)protection.
Why Many Prototypes Don’t Become Finished Products
So why is revolutionary innovation more feasible for prototypes than for high-quality, refined products?
Here’s why in my view.
Cost and yield rates: Prototypes don’t require cost control or high yield rates. A successful prototype may simply demonstrate the concept, but it doesn’t align with user expectations. Along with functionality and performance, users implicitly expect quality and reliability. Without the means to reduce production costs and improve the financial yield, neither the product nor the company will achieve profitability.
Complexity of refinement: Prototypes focus on technical breakthroughs alone, while refinement involves a much broader range of considerations. It typically requires extensive knowledge and large, diverse teams, whose collaboration presents far greater management and communication challenges than building the initial prototype.
Real-world application testing: Prototypes can be developed in isolation, realizing the designer’s vision. But refinement requires extensive field testing across a range of customer scenarios. For instance, in the prototype stage, we tested in a fixed lab environment. Engineers didn’t anticipate the need for 30kV ESD protection or potential interference issues customers might face due to various wireless sources.
Sustained team commitment: Many team members find the prototype stage exciting and fulfilling, but find the refinement process tedious. The process of product refinement demands patience, resilience, and a craftsman’s mindset on the part of the team.
Our Successful Journey from Prototype to Product
Creating a prototype represents only a small portion of the journey from concept to commercialization; in fact, it’s only about one percent of the effort. The remaining 99 percent lies in refining the product to enhance user experience, improve its yield and reliability, adapt it to diverse application scenarios, and meet global regulatory requirements.
With our W26 ring scanner, I’m proud to say we did just that, completing the journey from prototype to product that fills a market need.
Creating a prototype represents only a small portion of the journey from concept to commercialization; in fact, it’s only about one percent of the effort. The remaining 99 percent lies in refining the product to enhance user experience, improve its yield and reliability, adapt it to diverse application scenarios, and meet global regulatory requirements.
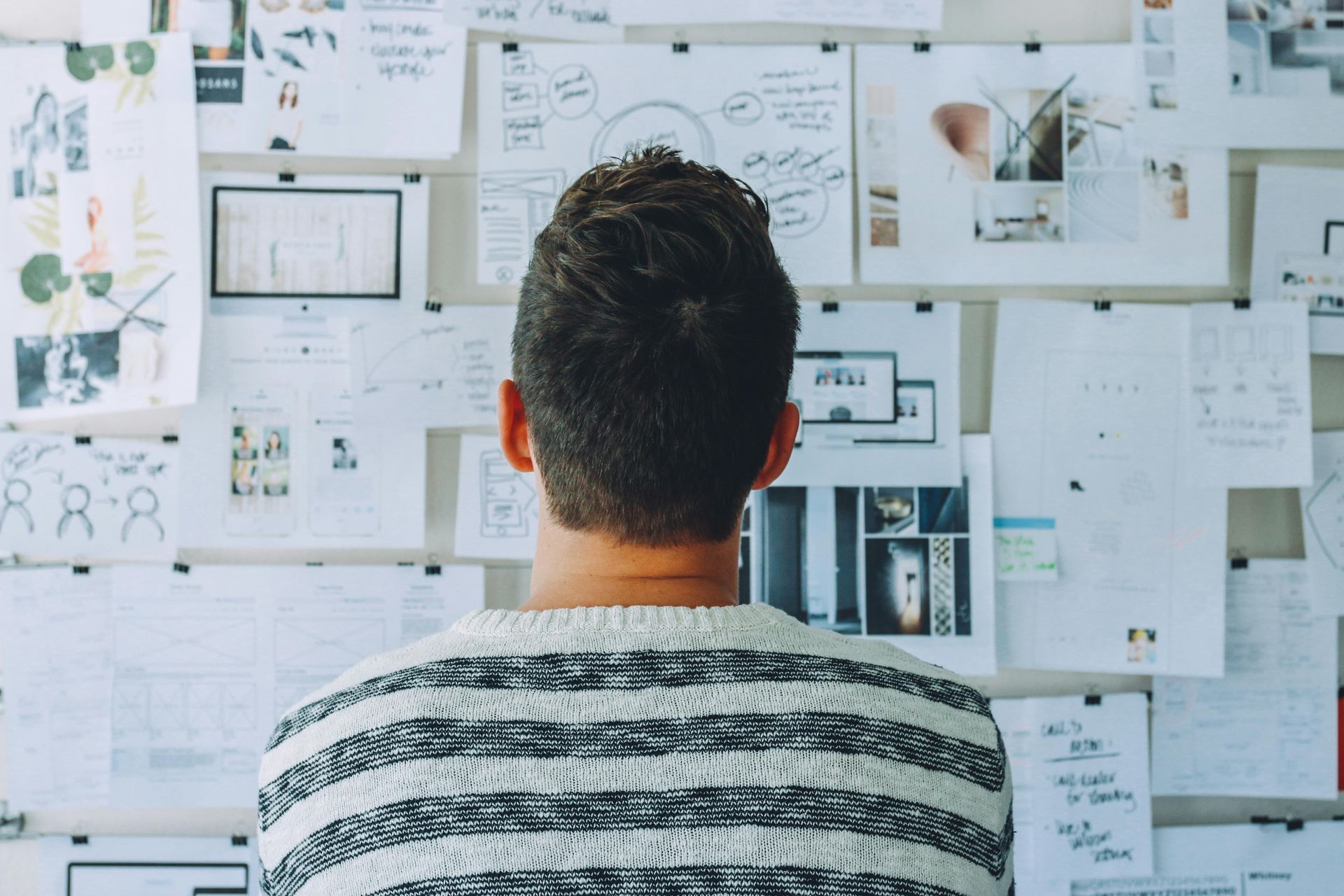
With our W26 ring scanner, I’m proud to say we did just that, completing the journey from prototype to product that fills a market need.
Product Link:
1. Ring Scanner - Plug & Play
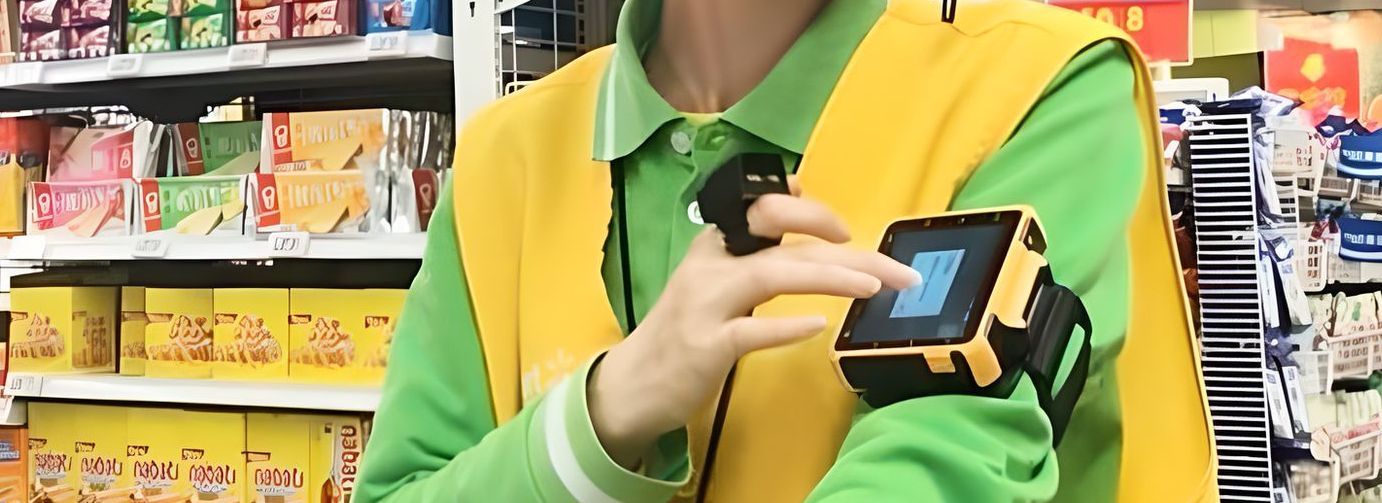
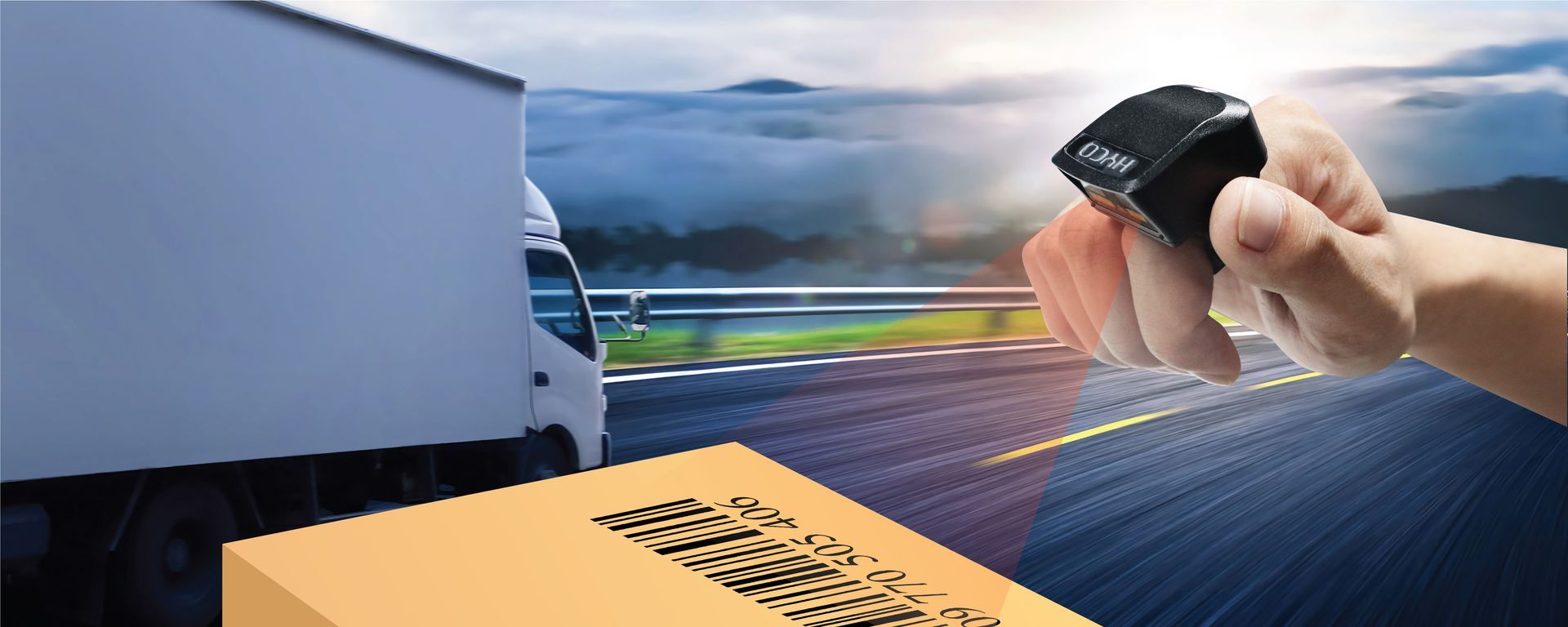
